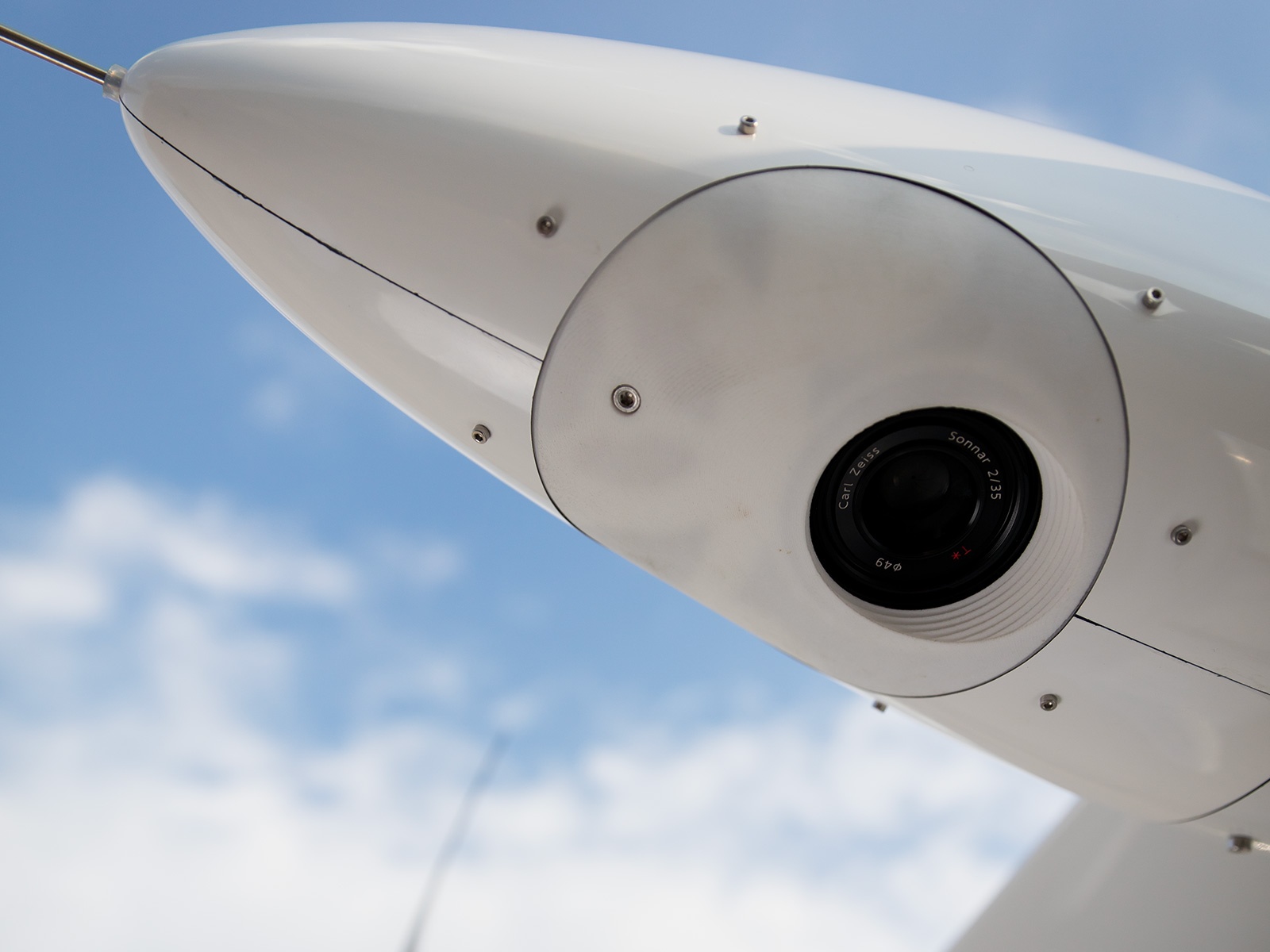
Like 3D printing, drone technology was also developed long before the general public was aware. While it may be surprising enough to find out that 3D printing was created decades ago, the first rudimentary drones came into inception well over a century ago.
Initially, the motivation behind conceptualizing drones was stealth, designing for the ability to perform surveillance or complete missions from overhead. Today, however, uses include:
- 3D printed aerial photography for a wide range of industries to include real-estate and insurance
- Commercial deliveries
- Crop spraying
- Geomapping of land for commercial endeavors
- Inspections of wind turbines and other machinery
- Military reconnaissance
- Monitoring of livestock and wildlife
- Search and rescue and delivery of supplies
- Surveillance for disaster management
The range of applications continues to grow, leading to a diverse number of choices in 3D printed drone design too.
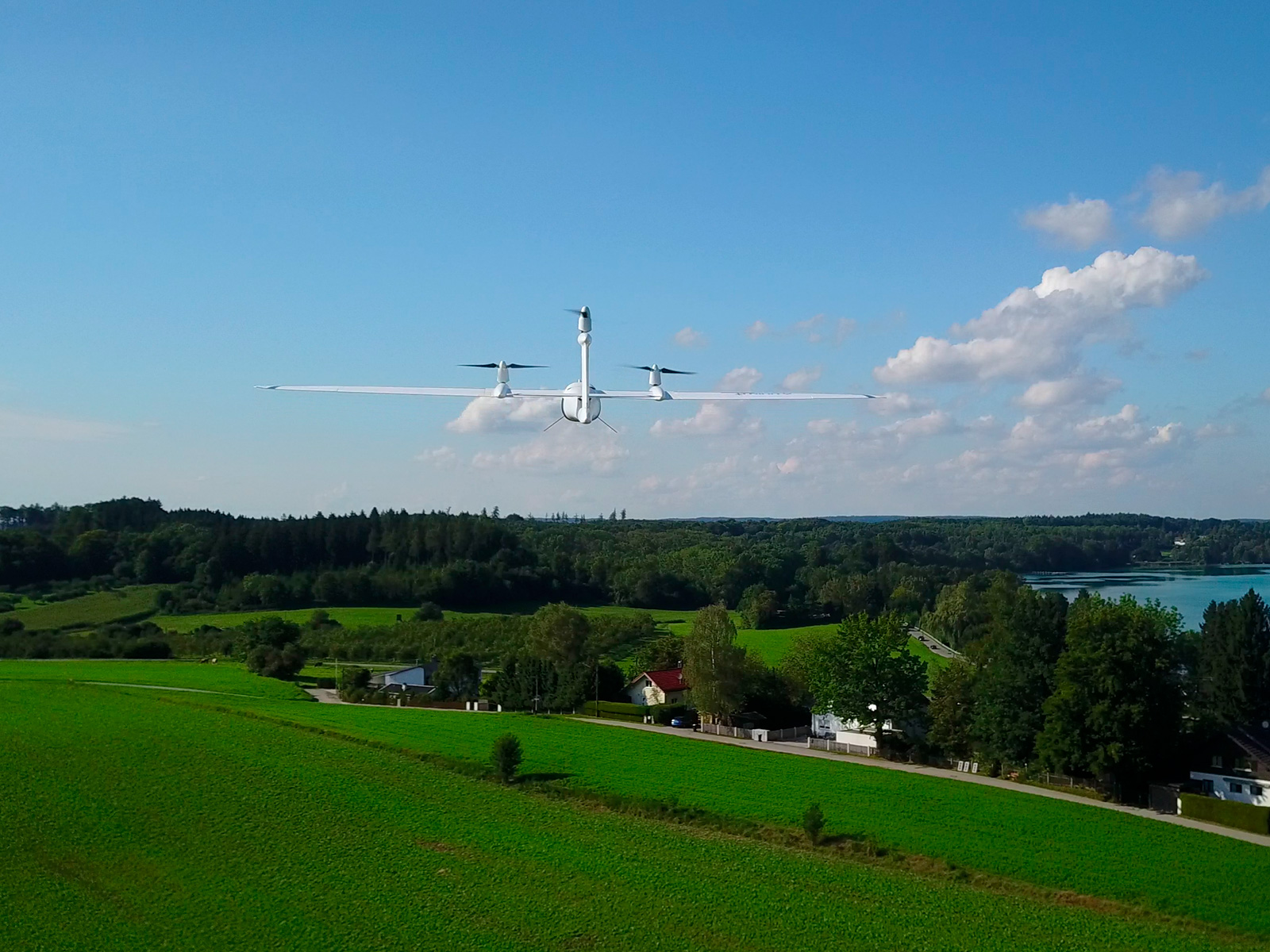
Light Weight and Low Assembly are Features Key to 3D Printed Drone Frames
Weight has been an issue in aeronautics since the Wright Brothers flew their first plane in Kitty Hawk back in 1903. Every material used was required to be strong, yet light in weight, whether wood or fabric. The fantasy of flight has yielded some incredible inventions throughout time, along with a variety of manufacturing methods. Flashing forward to the present, 3D printing and drone technology are a superb pair, allowing for nearly any design, accompanied by a growing list of advanced 3D printing materials and technology.
In designing 3D printed drone frames, lightweight materials offer the obvious ability to maintain their position in the sky; however, a lighter weight also means they can travel more efficiently and with more weight to be allotted for the rest of the payload. Shapeways has worked with customers like Quantum-Systems in optimizing 3D printed drones since they were founded in 2015. The Munich-based drone manufacturer saw the promise in 3D printing for prototypes and end-use parts right away.
In designing a shield for an antenna mounting on one of their drones, Quantum-Systems sought to optimize the part further in terms of weight. They continued to work with Shapeways on the design, and ended up reducing a 23-gram part by a substantial 8 grams. The end-product was the result of additional prototyping and experimentation, ultimately transforming the part from a traditional structure to a lightweight, honeycomb design.
3D printing is known for features such as the ability to perform rapid prototyping and make complex geometries like never before. The ability to reduce assemblies is extremely enticing to most manufacturers too though, leading them to explore technology like Multi Jet Fusion with materials like MJF PA12, allowing for interlocking components to be printed in one piece.
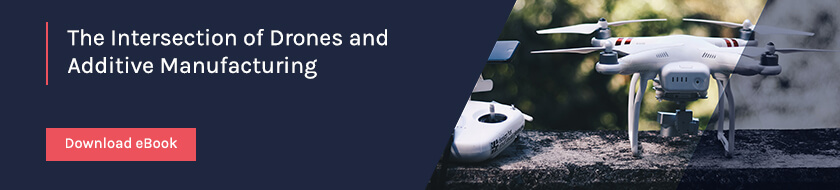
Developing and Testing 3D Printed Drone Prototypes
Although 3D printing was initially created as a rapid prototyping tool meant to speed up product development for industrial engineers, the technology has evolved into a comprehensive tool. For example, Shapeways customers may use Nylon 12 [Versatile Plastic] during development, ordering over a hundred iterations in different finishes and colors–and then they may go on to 3D print their functional, end-use products with the same materials and technology like Selective Laser Sintering. Proving the point further, recent research shows that 54 percent of engineers reported relying on 3D printing for functional parts.
Whether still engaged in prototyping or moving on to 3D printing end products, drone designers must plan for success by outlining the basics and then filling in the blanks as they move forward in customizing parts. This includes planning for the specific application and corresponding structure of the drone, and matching it with compatible materials and technology to ensure printability of the part.
Size limitations must be considered again for project requirements with 3D printed drone frames, but regulations must also be followed. As prototyping continues, the design team has to consider payload specifications beyond the weight of the drone, the camera, and any other built-in parts, along with any options for optimizing maneuverability. Beyond that, details for further efficiency must be included like blade structure, length, and efficiency. Many designers 3D print all of the housings for electronics, and that includes the remote control.
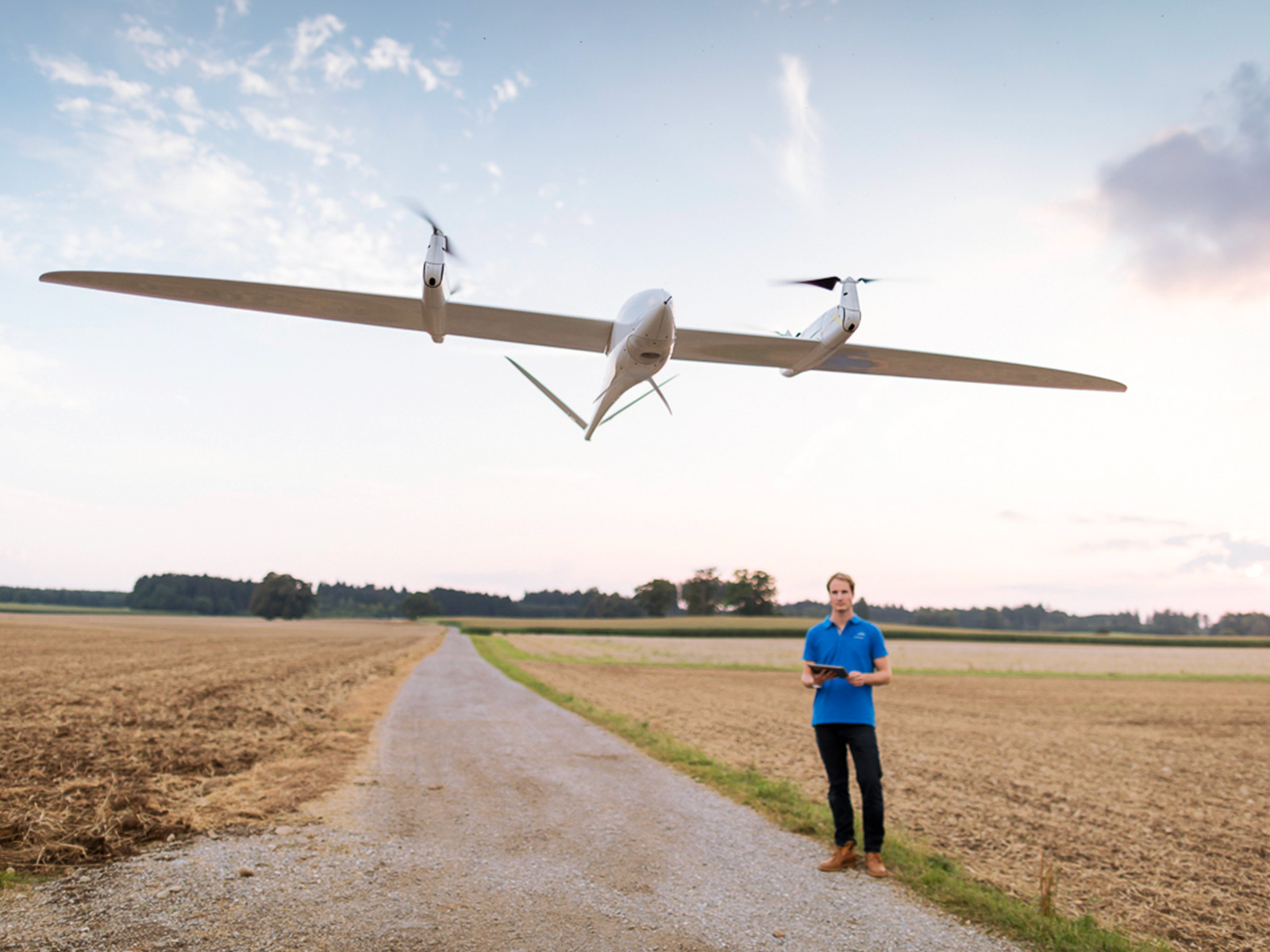
The Best 3D Print Materials for Drone Parts
3D printing technology offers even greater opportunity and freedom in design for drones, along with rapid prototyping and turnaround of end-use parts. At Shapeways, customers rely on a variety of resources for drone applications, depending on their exact needs.
Whether companies are still engaged in product development or manufacturing end-use parts, Shapeways offers a variety of advanced materials, to include:
- Nylon 12 [Versatile Plastic] with Selective Laser Sintering is one of the best 3D print materials for drone parts. This material is highly adaptable, offering elasticity for thinner parts, and rigid strength for thicker structures. Nylon 12 [Versatile Plastic] is offered in an array of colors for dyeing as well as finishes ranging from Natural to Smooth.
- Multi Jet Fusion Plastic PA12 is 3D printed with Multi Jet Fusion technology to create prototypes and functional products requiring both high strength and great accuracy. MJF PA12 and Multi Jet Fusion are extremely well-adapted for drone prototyping due to precision in parts, as well as the excellence offered in surface quality and texture.
- Resin-based materials for 3D printing with Stereolithography include Accura 60, Accura Xtreme, and Accura Xtreme White 200. SLA 3D printing offers accuracy, good mechanical qualities, and also nice smooth surface finishes which make it a popular choice for designers engaged in prototyping or 3D printing or end parts that require a more realistic look.
- Aluminum – This material (alloy AlSi10Mg, 10% Silicon 0.5% Mg) is favored for high-performance parts required for aircraft like 3D printed drones due to incredible strength and durability. Even better, Aluminum is lightweight enough to allow for maximum flying speed in UAVs. This material is 3D printed with Selective Laser Melting (SLM), a technology known for its ability to 3D print strong metal parts rapidly, and without tooling.
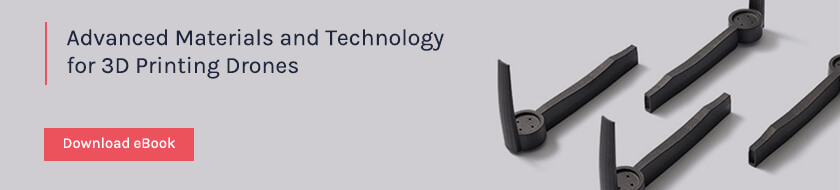
About Shapeways
Enjoy the benefits of this advanced technology and a wide range of materials from Shapeways for 3D printing your creations with accuracy, complex detail, and no minimum or limits in terms of mass customization or single part orders. Shapeways has worked with over 1 million customers in 160 countries to 3D print over 21 million parts! Read about case studies, find out more about Shapeways additive manufacturing solutions, and get instant quotes here.