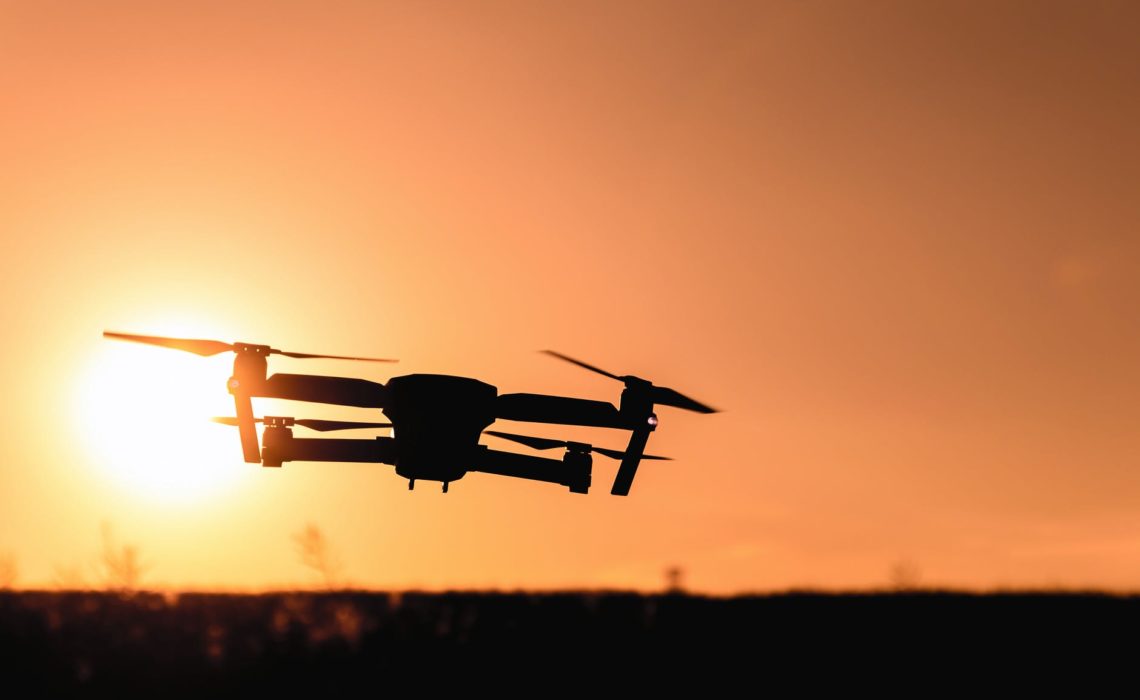
For centuries humans have built products that have been regarded as engineering marvels. We continually enhance and augment our skills to create complex designs and products that draw from the natural world.
Sustainability has always been at the center of nature’s design and this core logic has helped it to survive, sustain and grow. Humans have long strived to create something as complex as nature itself, not realizing the fact that even learning from nature is a big challenge.
Learning from nature is of utmost importance and this fact is emphasized by proponents of biomimicry. Biomimicry is a concept that has emerged as the savior in recent times and it talks about mimicking nature to build products. Biomimicry, coupled with the most powerful manufacturing technology of the recent time – 3D printing, can truly be applied today in real-world applications and its benefits can be enjoyed by generations to come.
What is Biomimicry?
Biomimicry, as defined by the Biomimicry Institute of Montana USA, is an approach to innovation that seeks sustainable solutions to human challenges by emulating nature’s time-tested patterns and strategies. Simply put, biomimicry (bio – nature & mimesis – imitation) means to mimic nature, though it is much more than that. By mimicking or imitating nature, we can build products that can sustain over longer periods of time, utilize fewer resources and be more efficient in its operations.
Biomimicry researchers and supporters believe that nature has already thrived for so many years and so it already has all the answers to create solutions that can sustain for the next billions of years. Animals, plants, and microbes are the consummate engineers. After billions of years of research and development, failures are fossils, and what surrounds us is the secret to survival.
Biomimicry & 3D printing, Together
Biomimicry deals with mimicking nature to create sustainable products. But the core problem lies in creating such products. With the restrictions faced by traditional manufacturing processes, the mimicry is not served well. Fortunately, this problem is solved by the latest manufacturing technique, 3D printing technology. With this combination, the opportunities are endless.
3D printing is by principle a process that replicates nature in how things are manufactured. Like in nature, any creation grows in small increments to subsequently form a larger and more complete object, the 3D printing technology also builds products in a step by step process from scratch.
The similarity is striking and is an exact match to the concept of biomimicry. Complex objects found in nature can now be easily manufactured through 3D printing technology and this can have a significant impact on the entire world. The fusion of biomimicry and 3D printing seems fairly obvious.
The natural combination is already being applied to create solutions that can impact product manufacturing. Let’s take a look at some of these real-world examples.
Honeycomb Patterns
The initial research in combining biomimicry with 3D printing brought the evolution of the honeycomb structures. This form of structure is used in the infill pattern and support structure pattern in 3D printed parts.
Unlike traditional processes, 3D printing can control the infill of any part. Instead of creating a fully solid product, a honeycomb pattern in an object lends greater strength while using less material. In general, most FFF 3D printed objects are only 20-30% full.
The honeycomb pattern obviously originated when engineers studied the cross-section of an actual honeycomb. You can imagine that they decided to experiment the same idea in 3D printing and it has been the go-to infill pattern since then for manufacturing strong parts.
Footwear
As it became an established fact that 3D printing can create any type of complex part, the use of lattice structure has rapidly been incorporated by companies far and wide. Footprint3D, a footwear company, created 3D printed insoles and midsoles which were inspired by insects.
The team observed the wings of insects to create a lattice design. The lattice structure is vital as the midsoles and insoles provide all the support for the feet and allow natural gait. The company can just scan a customer’s foot and automatically design the required structure. But it can also be modified as per individual user providing them with the most optimized and healthy walking experience. The nature-inspired structure is helping customers walk in their own natural way without harming their feet.
The soles were manufactured using a 3D printing technology called Selective Laser Sintering (SLS).
Using Fish Scales to Protect Soldiers
With an effort to work on protection based products like armor, researchers at Northeastern University College of Engineering are studying how nature is protecting itself. The researchers honed down on fishes to study their scales and how they not only offer flexibility but also stiffness. The researchers believe that theirs is a very unique approach to create armor. The team feels that nature provides a very important piece of information on how to develop armor. If they apply fish-based scales in specific places on the soft material layer, it makes the surface stiff instead of elastic.
According to researchers, “The next generation of armor systems are light, perform a lot of functions, and at the same time do not compromise on protection. And nature provides very important information in terms of armor development.”
But the researchers concluded that their research and the subsequent product will not be possible without the use of 3D printing and the variety of materials it provides, which allows people to overcome the limits of nature using its own patterns.
Graphene
Graphene is a naturally occurring material that has unique properties, namely being one of the strongest materials out there while also being extremely lightweight. Due to these properties, it is widely used in energy storage, optical electronics, composite materials, and biological engineering applications. Its outstanding ability to conduct heat, as well as electricity, enables it to be used in cars, buildings, filtration devices, and even airplanes.
But it used to be a very difficult material to be used and operated upon until 3D printing came along. MIT researchers are now able to create new graphene structures for 3D printing. Biomimicry allowed them to learn about the material and how to work with it. They used the 2D architecture of graphene in 3D structure to create spongy material that potentially can be a game-changer in additive manufacturing.