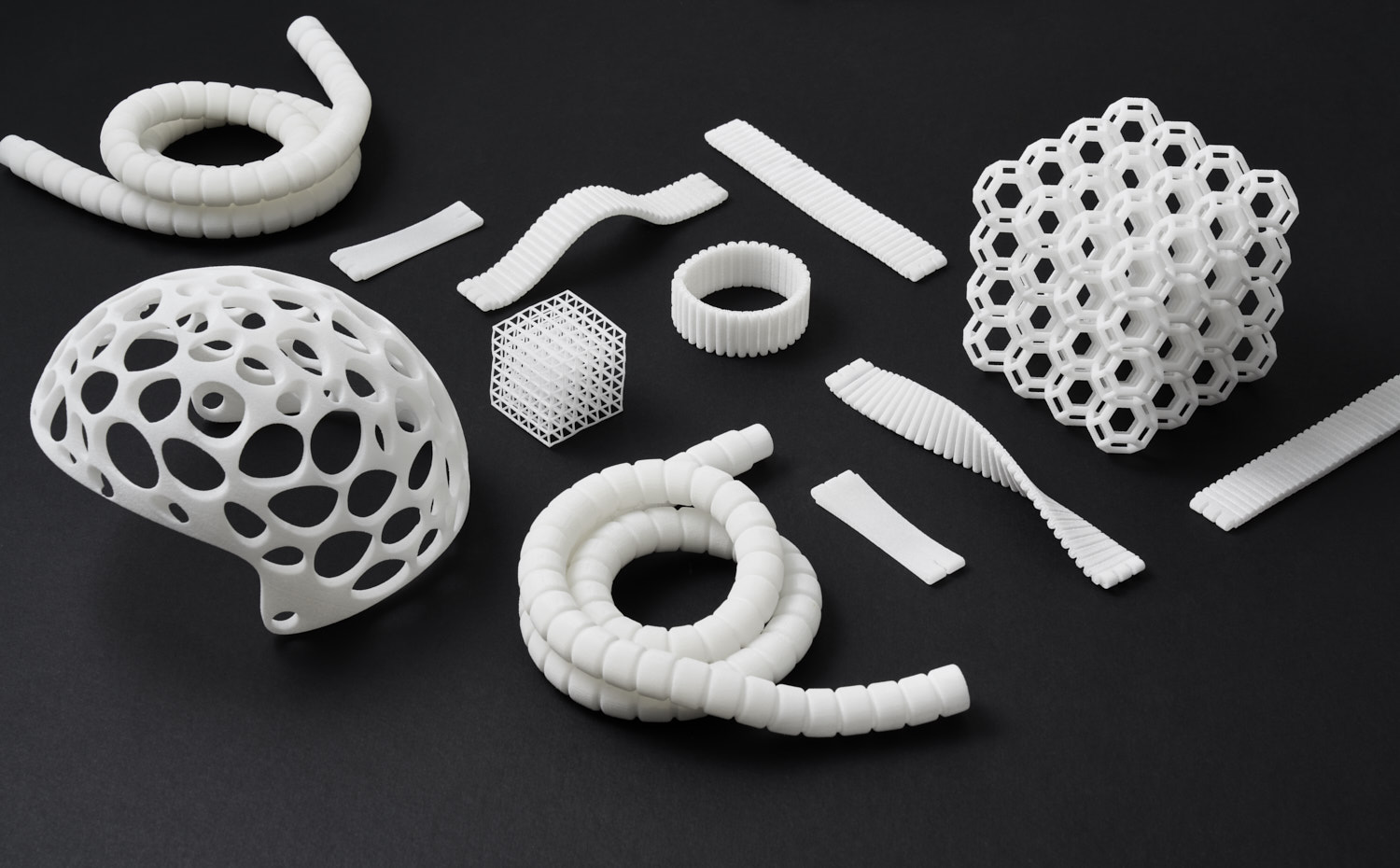
The who and why of 3D printing technologies
Most brilliant innovations come about not by whim or random tinkering, but need, whether on the individual, research, or commercial level. In the case of 3D printing, a spectacularly futuristic technique for rapid prototyping emerged from a few small homegrown labs, branching into a billion-dollar industry decades later—and captivating interest worldwide.
The history of the evolution of 3D printing is pretty expansive if you really dig into the powers-that-be pioneering the realm of astounding new technology. We’ll focus here on the main masterminds who gained attention in the 1980s as engineers on parallel paths. Chuck Hull, typically known as the inventor of 3D printing, was responsible for stereolithography (SLA) technology.
Dr. Carl Deckard and Dr. Joe Beaman, associated with both University of Texas at Austin and the Defense Advanced Research Projects Agency (DARPA), patented selective laser sintering (SLS) technology. Later, they formed DTM Corporation, only to be acquired by 3D Systems in 2001, with Hull at the helm as co-founder and CTO. Not to be left out of the timeline, Scott Crump also patented FDM 3D printing in 1989, going on to found Stratasys.
While these developments and contributions were immense—fueling some of the industry heavy hitters we still see going strong in 3D printing today—the benefits and true impact were not felt around the world until patents began running out (like the SLS patent in 2014) and 3D printing technology became more accessible, affordable, and attractive as an option for the mainstream.
How it works: SLS is much simpler than you may think
SLS technology was created to expand capabilities in product development. Like most other 3D printing methods, it was initially meant for rapid prototyping. As users began experimenting further, SLS became clearly advantageous for industrial needs as the lasers melting powders are fast and powerful, resulting in accurate end-use parts that are strong and isotropic (possessing the same properties when measured in varying directions). Users do not have to be as focused on making up for a lack in mechanical properties either as SLS parts tend to offer excellence in tensile strength (resistance to breaking) and modulus (stiffness).
There are countless amazing products that are manufactured via additive manufacturing (AM) processes today, but there are also so many acronyms that it is easy to become confused within the sea of innovation and industrial jargon. SLS technology is powder-based for fabrication of structures via laser curing, while stereolithography (SLA)—and its similar cousin, digital light processing, (DLP)—are both liquid, resin-based technologies, with DLP relying on a projector instead of lasers. Adding another technological cousin to the mix, selective laser melting (SLM) goes beyond sintering. Often used for pure metals as well as alloys, all the material is melted together into a homogenous part.
Ultimately though, the SLS 3D printer remains at the top of the hierarchy for additive manufacturing, known as a powerhouse of hardware allowing users to go beyond the expected limits in manufacturing. Most SLS 3D printers are enormous in size compared to what you may be used to if you have been printing at the desktop. In fact, the average build size is around 300 x 300 x 300 mm with a layer thickness of 100 – 120 microns (with larger machines boasting much broader capabilities), and average builds of 500 to 1000 parts. The process is disarmingly simple though, as a thin layer of powder is automatically distributed onto the build plate. This material, usually nylon powder, is then (thus the name) selectively sintered layer by layer and point by point as designated by the 3D design uploaded into the accompanying software.
The pros and cons of SLS 3D printing
One of the greatest benefits in SLS 3D printing is the outstanding ability to avoid the use of supports. Surrounding and lingering powder bolster prints in progress so they do not require added stability or structures, replacing previous, major headaches for users with much more design freedom. All this extra powder can be re-used in following productions too, but it must be mixed with virgin powder, which is usually recommended as a 50/50 mix at minimum. The less recycled powder there is—the higher in quality the part will be. If you see a perfect part, there is a chance that very little recycled powder was used, and in fact, the part may have indeed been created with 100% virgin powder.
Rather than printing one tiny part at a time, SLS technology also allows you to “nest,” meaning that you can cram multiple parts into one build—saving a significant amount of time. This is a good balance in light of one of the drawbacks to using SLS technology: parts are usually not ready immediately and almost always require post processing. While such work may be tedious at times, these finishing efforts are where the ultimate perfection—and often additional customizations occur.
Once 3D printed and cooled, the operator retrieves the parts from the bed of powder and moves them to an area set up for post processing. Completed parts must be cooled, then thoroughly dusted off in a cleaning station, and often this requires the use of compressed air to get rid of large volumes of excess powder. Because surfaces may still be rough at first, the user/operator may need to sandblast the part for smoothing too.
If color is desired, one of the great benefits in SLS parts is that they can be dyed according to a palette of hues; for example, at Shapeways, the Nylon 12 material (also known as Strong and Flexible, PA12, Polyamide, and PA2200) is offered in natural white, but parts can also be dyed in black, pink, red, orange, yellow, green, blue, and purple. Because of higher porosity (also responsible for those initial rough surfaces in SLS prints), the color is easily saturated. Parts may also be enameled, coated with metal or other powders, or even painted.
While users may be able to perform some customizations from the home workshop, overall, SLS 3D printing requires experience and skill in operations—despite the streamlined process. Typical challenges arise and must be compensated for with proper settings and monitoring. Print times can be lengthy, and post-processing must be anticipated. There can be drawbacks in working with specific powders too, causing difficulty in printing larger, flatter parts.
Shrinkage is an issue that continues to be a challenge for any type of SLS technology due to the intrinsic qualities of nylon powder. This is where expertise is required not only in terms of 3D printing as a whole (keeping in mind that other types of materials cause shrinkage too), but particularly in SLS. Relying on the highest quality in hardware and software, Shapeways is able to avoid both shrinkage and warping by monitoring the cooling process closely for uniformity in parts. Over-sintering is another challenge that must be considered too, as extraneous powder surrounding the parts can become fused while printing.
Why SLS is so important to critical applications
The versatility of SLS printing is impressive, demonstrated by the wide range of applications currently benefiting from these 3D printed prototypes and end parts. One of the most exciting industries to use services from Shapeways for SLS printing is the medical field. And while organizations like NASA may use SLS printing to produce a mind-boggling array of parts for space travel (and some companies may even build entire rockets) what is happening in medicine is particularly important as some of the models and devices being created now have the ability not just to change lives, but in some cases—save them.
Automotive companies have been using SLS printing for decades too. While they may use additive manufacturing to fabricate spectacular prototypes, car manufacturers (as well as rail companies) are now relying on such technology for functional parts—whether under the hood or in the interior. Many different mechanical parts can be digitally fabricated too, such as air vents, gaskets, and seals. Industrial users choose SLS printing because they need strength and precision for critical components.
3D scanning of obsolete parts in many cases leads to success in restoration projects too as designers and engineers find that they can copy a part (even tweak it to make it better in some cases) that was made a long time ago, print it right out, and avoid endless hours trying to track down something extremely difficult to find—or worse, no longer available. While this type of work is not exactly new in the automotive realm, other industries like railways are also getting in on the action as they find realistic, affordable methods for maintaining important parts that may not have needed replacing for decades.
Who is using SLS technology from Shapeways—and why?
Customers have relied on Shapeways for SLS printing and the use of accompanying materials for many years, and in a wide range of unique applications. Here are two examples showcasing the flexibility of this material in providing precision printing for both small and large parts:
- Working with one architectural design customer in the Bay Area of California, Shapeways 3D printed a lavish, six-foot-long vanity for a children’s bathroom in a luxury home remodel. The focus was on durability and longevity, specifically because of the amount of wear and tear expected during years of use by the younger generation. SLS technology (using Nylon 12 as the material) was chosen for this project due to the larger scale of printing and intense customization required.
- Another long-term customer of Shapeways chose SLS printing for designer jewelry made in the Netherlands. Dutch design duo Hanno Groen and Joanna Boothman of Amsterdam were able to mix SLS technology in creating their customized Creatures bracelet series—also featuring handcrafted touches like interior upholstered leather and gold-plated studs bearing their emblem. Again, both luxury and durability are highlighted as the bracelets are meant to be valued over the years as keepsakes. Nylon 12 was used in order to fabricate extremely lightweight jewelry with the flexibility required for finishing, as well as excellence in customer fit and comfort.
Materials offered by Shapeways
Are you interested in 3D printing industrial parts? Check out the following materials offered for SLS printing via Shapeways services:
Nylon 11 in natural white finish is suitable for a variety of applications such as:
- Auto parts
- Mechanical parts
- Sports equipment
- Other components requiring strength and impact-resistance
Nylon 12 may be used for the following:
- Hinges, springs, and cases
- Prosthetics
- Models with interlocking parts
- Models which may require interlocking parts as well as strength and stiffness
Thermoplastic polyurethane available in off-white color is suitable for products requiring elasticity, including:
- Medical models
- Automotive parts
- Hoses and seals
- Footwear
SLS will continue to play a starring role in future trends
Resin-based processes like SLA and powder-based SLS all compete for users in terms of their ability to create complex geometries for prototyping and customized parts. One difference that stands out, however, is that while SLA printing may be relied on for making smaller parts and intricate molds to be used in injection molding—SLS can be used to replace injection molding in lower-volume productions. While these trends continue into 2021, as new software and hardware continue to hit the market, users can look forward to a wide range of more scalable options to include more streamlined automation, higher build volumes, and of course, the ability to increase build rates when using multiple lasers.
Today, technology like SLS, SLA, and DLP are even accessible at the desktop level. These more affordable options have become available under $10,000 in some cases (plus the expense of nylon powder for sintering), while commercial hardware meant for serious industrial use of high-performance parts will cost as much as a few hundred thousand dollars. The difference is that desktop machines are not yet capable of bulk producing impeccable, industrial-quality parts at this point.
At the desktop level, while you may be able to produce one quality part, it will in most cases be difficult to “nest,” and print multiple parts in the build chamber at one, meaning that you lose out on one of the greatest benefits in SLS printing. Along with that, you must also deal with the inconvenience of dealing with leftover powder once the print is complete. The bottom line is that SLS printing technology is generally considered highly industrial—and users must be well-trained in such operations.
3D printing services from Shapeways such as SLS printing allow you to reap the rewards of high-performance, quality materials without having to invest your business capital in the powerful hardware, software, and materials required for your build. For more custom solutions to fit your additive manufacturing needs, Shapeways is here to help.