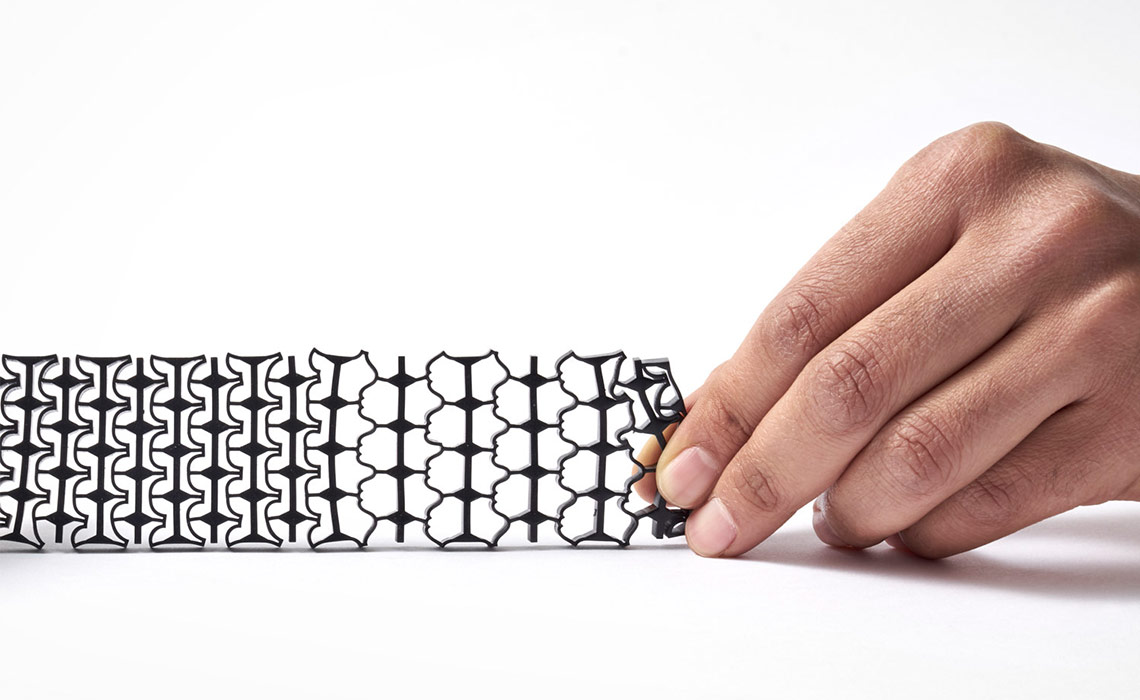
Research shows that the global market for additive manufacturing will reach $23.33 billion by 2021.
From the aerospace industry to the medical field, there are myriad sectors that are leveraging this technology to speed production time, meet tough performance standards and expand the realm of what’s considered possible within their niche.
Along the way, similar methods and processes have emerged, including injection molding.
While the two techniques are similar in nature, additive manufacturing and injection molding are not synonyms. Today, we’re breaking down the differences between the two. We’ll also reveal which one wins out as being the most effective way to meet robust manufacturing requirements.
Ready to learn more? Let’s get started!
What is Additive Manufacturing?
While it’s quickly becoming a common term, most people still recognize additive manufacturing by one of its most popular subsets: 3D printing.
Similar to the way a normal printer works, a 3D printer hooks into a computer and connects to a specific kind of Computer-Aided Design, or CAD, software.
Engineers can use the CAD software to create a detailed sketch of the product they want to produce. Then, the additive manufacturing machine reads this CAD data and begins the complex layering solution.
In addition to 3D printing, the additive manufacturing umbrella also encompasses other innovative technologies, including:
- Rapid Prototyping (RP)
- Layered Manufacturing
- Additive Fabrication
- Direct Digital Manufacturing (DDM)
Benefits of Additive Manufacturing
Why should forward-thinking B2B leaders look to additive manufacturing to improve efficiencies? The answer is simple: There’s virtually no limit to what the technology can do.
In its infancy, rapid prototyping was one of the earliest uses of additive manufacturing. At this time, business leaders mostly looked to the process as a way to facilitate more robust preproduction visualization models.
Now? The technology is leveraged around the world to create durable, reliable end-use products across the following industries, and others:
- Aircraft
- Medical Implants
- Dental Restorations
- Automobiles
- Retail Fashion Products
Let’s take a look at five distinct benefits that additive manufacturing can provide regardless of the specific application.
Lower Cost of Entry
When it first came on the scene in the 1980s, additive manufacturing carried a price tag that most small-to-medium (SMB) business owners struggled to afford. These high costs were primarily attributed to the sophisticated machinery required to do the work.
As innovation soars around the world, it comes as no surprise that additive manufacturing is becoming more economical.
In addition, these machines allow business leaders to scale up production without cutting into capital or making sweeping organizational changes. In this way, manufacturers can use additive manufacturing to quicken the pace and profitability of their business model at a more manageable price point.
Easier and Quicker Revisions
While the design is meant to create end products, additive manufacturing does so in a way that exceeds normal warehouse limits. This is especially beneficial when it comes to creative exploration.
With this machinery, workers can create different versions of designs without placing too much emphasis on timeline or pricing. Years ago, if any changes occurred to a static design during production, even the slightest one could ramp up costs and delay entire projects.
Less Overall Waste
Traditional manufacturing methods were notoriously wasteful, paying little mind to the impact that widespread warehouse efforts had on the environment.
Take a milling machine for instance. Not too long ago, any shavings or kindling that the machine produced would be discarded as waste.
Now, additive manufacturing is transforming the way the milling process works. Rather than cutting down a larger block to size, it builds the block to the appropriate measurements, adding layers one by one until achieving the ideal dimensions.
For this reason, experts from the U.S. Department of Energy (DOE) estimate that additive machinery can help organizations reduce their waste levels and material costs up to 90%!
Lower Energy Costs
Along the same lines, additive manufacturing also helps to streamline and simplify the production process, which saves B2B organizations a substantial amount of energy.
In addition to efficiencies gained in new system development, the process can also transform end-of-life products, extending their use for far longer.
The best part? This process only requires a small fraction of the energy that would be necessary to create an entirely new part.
Simplified Team Training
If the idea of training your teams on the ins and outs of additive manufacturing sounds daunting, take heart.
Now, there are more programs, resources, and tools than ever before that simplify the complex process, making it accessible to employees with varying degrees of technical knowledge and competency.
What is Injection Molding?
Now that we’ve covered what additive manufacturing entails, what about injection molding?
In short, this is a mass-manufacturing process that involves injecting molten material into a preformed mold to create a new product.
Some of the most common materials used in this process include:
- Metals
- Elastomers
- Confections
- Glasses
- Thermoplastic polymers
- Thermosetting polymers
As this process relies on a single mold design, it’s a common method for professionals in the mass production industry who need the same part made thousands or even millions of times in order.
Benefits of Injection Molding
Now, let’s explore a few benefits that injection molding can provide for those in this sector.
Scalability
Injection molding makes it easy to scale production en masse.
After you’ve paid the price to create the molds and initiate the process, other costs remain relatively low. Moreover, prices continue to drop as you amplify the number of total parts produced.
Less Waste and Lower Scrap Rates
Compared to other manufacturing processes, such as CNC machining, injection molding doesn’t cut away as much on an original plastic sheet or block. This keeps waste and scrap rates as low as possible.
Still, the process isn’t totally scrap-free. If any waste does occur during the injection molding manufacturing, it happens at four main checkpoints, including:
- The runners
- The spruce
- The gate locations
- Excess material leaking out of the part cavity
Repetitive Reproduction
If you’re looking to create a slew of products that all look the same, injection molding can fit the bill. Because you’re working from one central mold, Part #5,000 should (in theory) look the same as Part #1.
Along the way, strength and product reliability doesn’t wane. In fact, injection molding can create some of the toughest, most durable products in the world. Depending on customer needs, designers can adjust the integrating ribs or gussets within each mold to create or remove flexibility.
In a high-volume production environment, this can be a major plus, enhancing both brand consistency and product reliability.
Ability to Mix Plastic Types
Through a process known as co-injection molding, workers can utilize different types of plastic simultaneously as required. This can open up new design possibilities, speed production time and help lower overall costs.
In addition, there is also a wide variety of coloring systems to choose from when creating your plastic resign design.
Quick Production Times
Compared to other manufacturing methods, injection molding is quick. Mere seconds separate new filing cycles, enabling workers to produce more molds in a shorter period of time.
As such, this efficiency increases revenue potential and profit margins, and businesses can pass these savings on to their customers.
Why Additive Manufacturing Reigns Supreme
Now that we’ve discussed some of the benefits that each manufacturing process provides, which one is ideal for your environment?
In most cases, the answer is additive manufacturing. Let’s review a few reasons why.
Volume
If you have a high-production environment, you can gain some economies of scale with injection molding. Still, those savings begin to wane when your part volume dips. Suddenly, prices go up and the practicality of the setup is lessened.
In years past, additive manufacturing struggled to keep pace with high-volume runs. However, there are new innovations, such as Multi-Jet Fusion (MJF) printers, that enable volumetric optimization, or the ability to print along the X, Y, and Z axes.
Now, this process is just as capable of meeting high-volume demands, while also being just as useful and economical when needs scale back down.
Initial Costs
With injection molding, you’ll put down a substantial investment when you pay to create the initial mold, sometimes to the tune of tens of thousands of dollars. If you make a mass number of parts, you may be able to earn some of that money back through efficiencies.
On the other hand, additive manufacturing has very little up-front costs, as there is no mold. Instead, users create and manipulate the digital file to perfect their design.
Change Requests
As discussed, it’s much easier to accommodate a change request within an additive manufacturing environment than it is with injection molding.
In many cases, workers would need to create an entirely new mold to meet project demands. Designers working with a CAD file can make the adjustments on a computer in seconds.
Design Complexity
Working with an intricate product design? If so, keep in mind that this complexity will translate into higher costs for mold production. In turn, your overall costs amplify.
There are some designs you might not even be able to attempt in an injection molding environment given the sky-high price point.
Conversely, additive manufacturing enables designers to create sophisticated, highly detailed products with ease, all while keeping you within your desired budget. A few of the complex designs you can tackle include:
- Difficult details
- Lattice structures
- Parts within parts
Production Speed
Total production times for injection molding can vary from project to project. Workers have to create the prototype, design the mold, and tend to other pre-production requirements. After the actual injections are finished, the rest of the production can move fairly quickly.
Still, injection molding still requires a post-processing period. During this time, workers may need to break larger parts into smaller components to be produced and assembled later.
With additive manufacturing, the only time restraint you’re working under is how long it takes the printer to create the object, plus any minimal post-processing required. Here again, MJF can help quicken printing time.
Find Your Top Manufacturing Solution Today
Are you ready to try your hand at a 3D printing manufacturing solution? If so, we’d love to help. Our platform allows users to turn their models and ideas into high-quality 3D prints available in a range of materials and finishes.
Contact us today to get the process started and let’s create something great together.