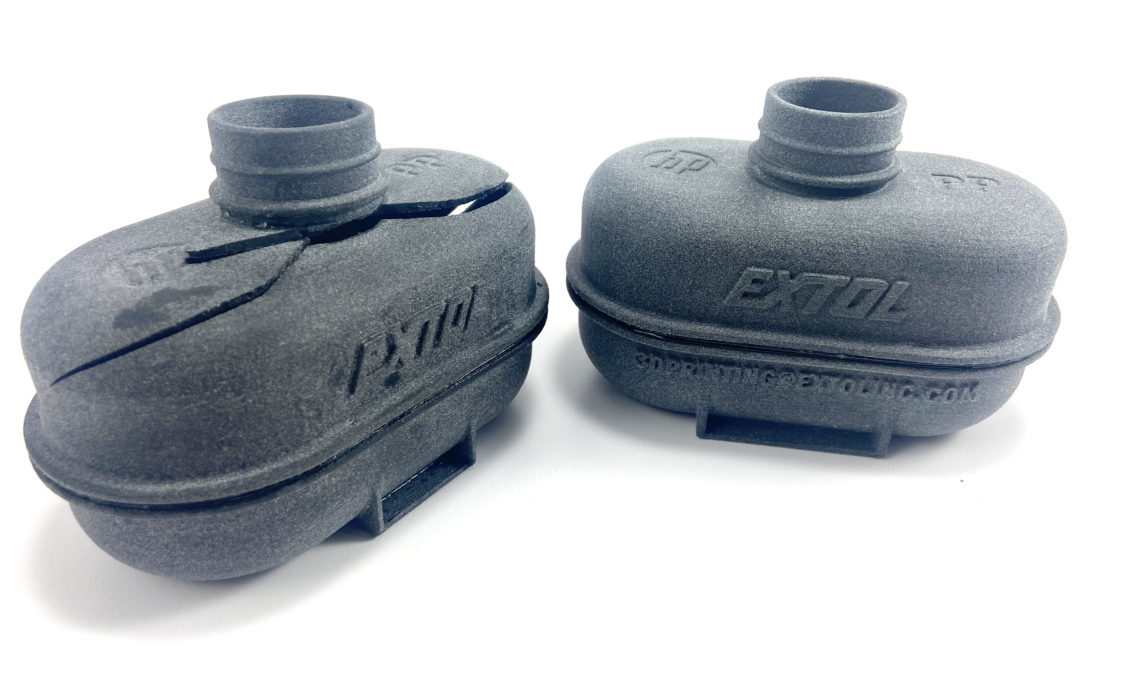
Polypropylene (PP) is the most prominent thermoplastic in traditional manufacturing, boasting huge annual demand worldwide that now also extends to additive manufacturing—prompting an intuitive partnership between Shapeways and BASF. Operating on a co-branded website, Shapeways and global startup Forward AM by BASF 3D Printing Solutions are working together to further empower customers 3D printing on the industrial level.
Forward AM by BASF is directed under the guidance of its mother company BASF in a charter to offer advanced materials, service solutions, and affordability through scale to enable taking additive manufacturing from simply a prototyping tool to production.
“The development of Polypropylene grades for powder based additive manufacturing was our logical step towards industrial production with 3D printing, especially in the automotive industry,” commented Christian Reinhardt, Global Automotive lead for BASF Forward AM. “From now on engineers can finally work with materials they are used to and don’t have to find workarounds for 3D printed applications anymore.”
Economics and Sustainability
The Forward AM PP is highly recyclable in both SLS (Selective Laser Sintering) and MJF (Multi-Jet Fusion) processes. This supports sustainability, limits waste, and keeps part costs very low.
BASF 3D Printing Solutions is committed to the industrialization of 3D printing for manufacturing. The affordability of 3D Printing materials will drive industrialization, and BASF has the capacity to manufacture powder at large scale, driving affordability. This dramatically moves the needle in the favor of AM for higher and higher volume runs where historically injection molding might have been chosen outside of prototyping.
“The ability to validate Polypropylene prototypes in the same base material as production enables cost and time saving opportunities for all customers,” said Aaron DeLong, Solutions Architect for HP. “Further, this breakthrough provides enhanced saving opportunities in bridge production, full production, and service applications.”
PP can also be an effective replacement for PA12 prototyping parts to bring about savings of 25%- 50%.
Performance
“In combination with Digital Printing, we see the BASF PP material as a game changer in the automotive industry to give OEMs more flexibility, leading to a greater focus on product-level features and increasing the speed of innovation.” – David Tucker, Director of Digital Solutions at Forecast3D.
BASF PP printed parts provide key advantages:
- Chemical Resistance. The material produces durable production parts for automotive applications.
- High ductility and toughness. Industrial applications benefit from the ability of the PP to provide damping and shock absorption.
- High burst pressure resistance. Unlike most printed powderbed technologies, the Forward AM PP powders are not inherently porous.
- Water resistant and watertight. Because PP is naturally water resistant, and the printing process makes parts watertight, it can be used in outdoor applications or where water tightness is needed.
Functionality
Forward AM PP printed parts can be welded just as IM parts are welded. This enables the opportunity for a multitude of functional production parts like tanks and reservoirs, tubes, and piping systems.
You can combine AM parts with IM parts or with custom fittings. Large parts that extend beyond a normal AM build volume can be produced by welding pieces together. PP enables light-weighting because of its low density which is often a driver in the transportation industry for fuel economy.
Applications
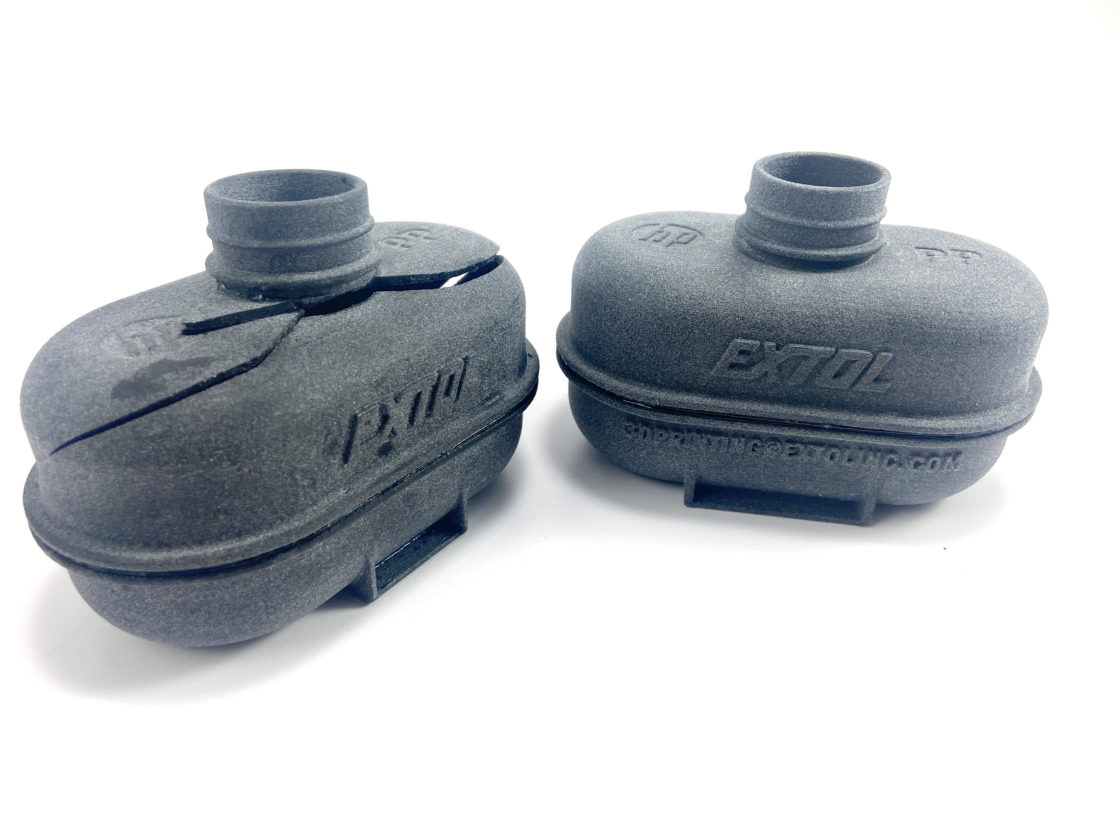
- Prototype bottle – this can be used in automotive test applications, printed in two parts and plate welded together. Passed pressure tests and brought development time from four weeks to four days.
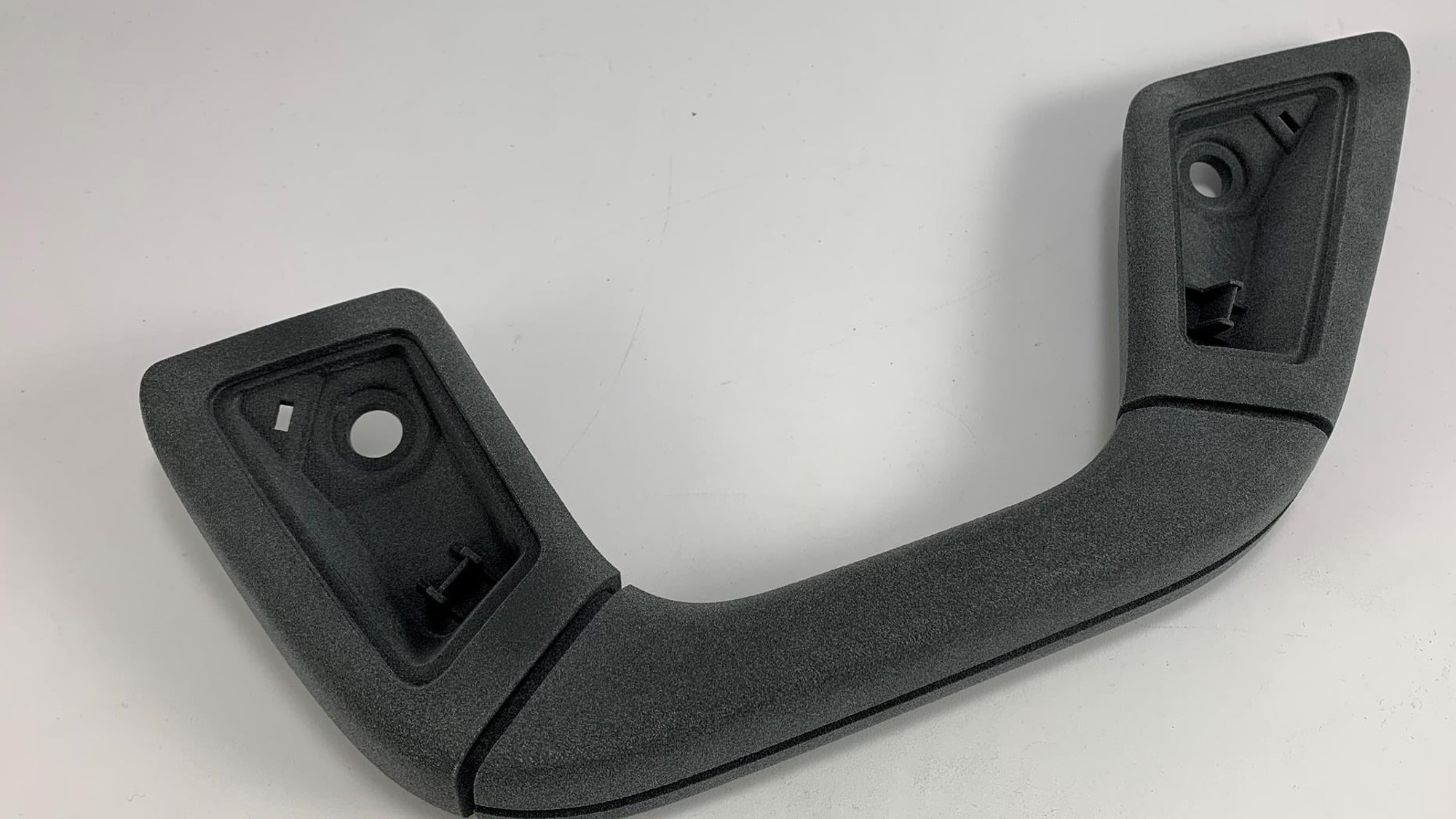
- Grab handle — meant for design validation applications for low volume premium vehicles. Printed complete sets for testing and production line acceleration. Saved estimated $15,000 tooling costs for design validation.
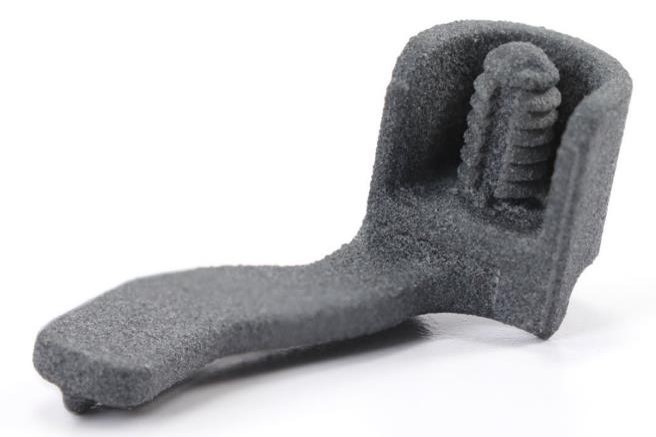
- Respirator fastener – completed a Covid response project. The customer was able to scale quickly, producing 28,000 parts in 3 weeks saving an estimated $10,000 in tooling. The strength and ductility of PP made the “Christmas tree” fastener functional.
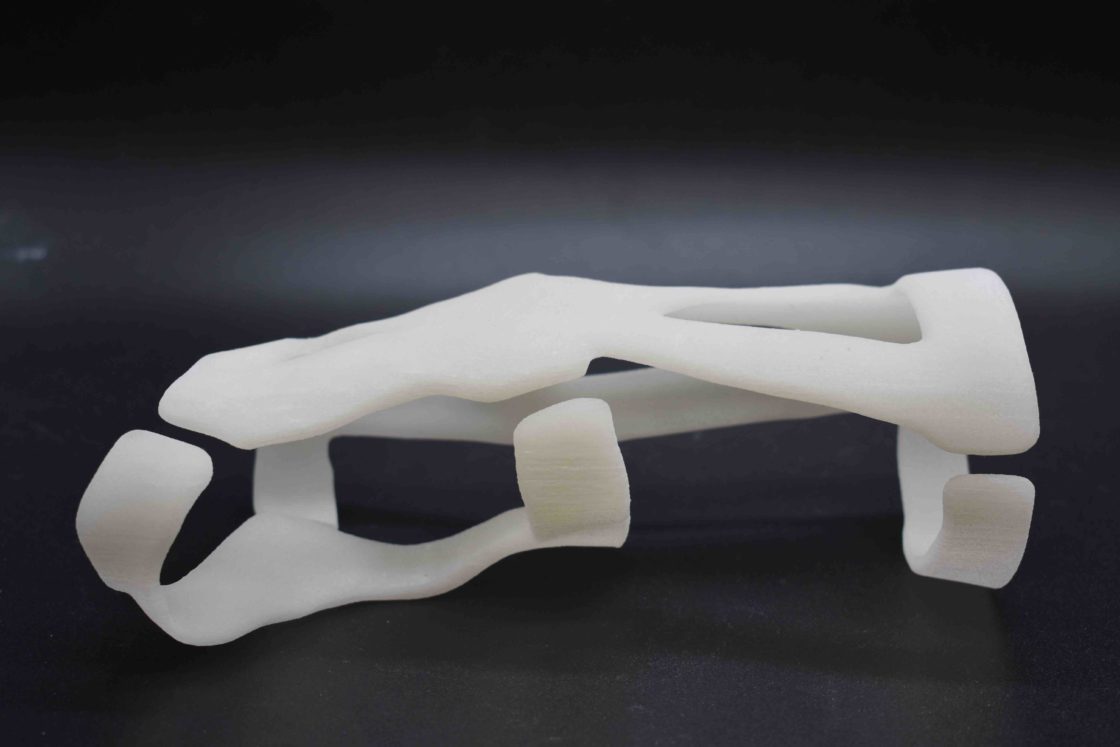
- PP wrist casts — promote comfortable healing. The cast is produced at a clinic or hospital without the challenges of a traditional gypsum cast; it can be slipped off and on and allows for ease of maintaining bandages underneath.
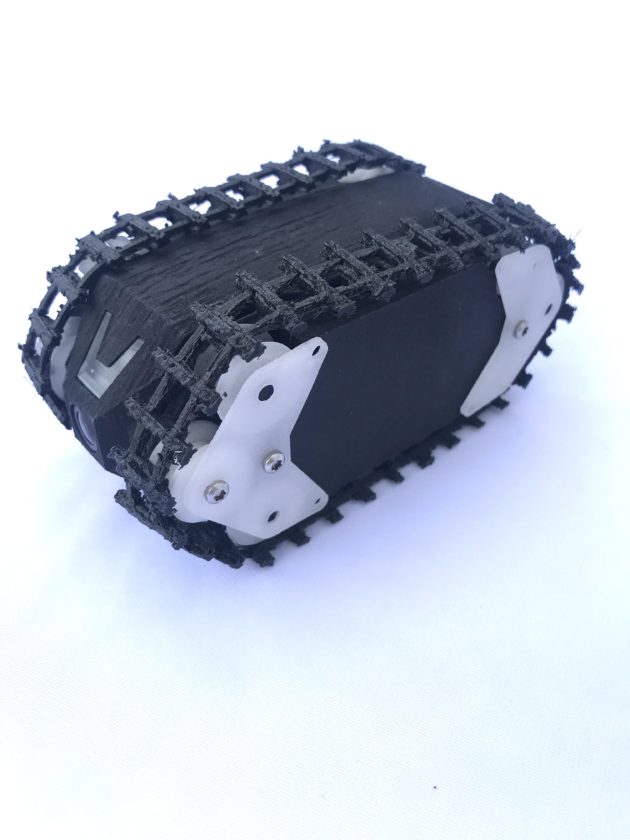
- Remote control inspection device – product development. Developed from prototype to production with all custom parts printed in PP for manufacturing. SLS PP saved 12 weeks in design time and $33k in IM tool costs.
Industrialization
BASF strives to leave the equipment choice to the customer by providing powders that work well across powderbed technologies. We think that this is another step in the right direction towards industrialization of AM. Users can process our PP powders on either HP’s MJF technology or a variety of SLS systems depending on what your preferences and specific needs are.
Many of our customers prefer to outsource their printing to service bureaus either in the ramp up stage or for long term manufacturing. This can be a huge benefit to limit capital expenditure, increase flexibility in manufacturing volumes, or simply to harness expertise that might not be a core competency. The network of service bureaus able to offer the BASF-manufactured PP powder is being built up at service providers like Peridot, Extol, and Forecast3D to start. For one-stop shopping, it is also possible to access PP and many other BASF materials through the Shapeways BASF portal.